Confusing and complicated.
These are two words that can frequently describe the selection of equipment in construction that is suitable for working at height. With so many types of machines available — each with a variety of models, specifications, and attachments — how do you know which is the best fit for your job?
On top of that, the pressures of intense deadlines can sometimes drive contractors to assume another piece of equipment already on site will make due.

However, using a machine that is not designed for the work is inefficient and dangerous, says Brad Mellott, product training specialist for JLG Industries.
“If they’ve chosen the wrong machine for the job, the ultimate end result could be injuries or fatalities,” he says.
With the proper planning and site assessments, contractors can avoid these significant consequences by selecting access equipment that will help keep their crews productive and safe.
In this article, find out what questions you need to ask and how to appropriately evaluate which machine is the right one for the task at hand.
Selecting a Telehandler vs. Crane
Increasingly, OEMs are introducing higher-capacity telehandlers as crane alternatives. Telehandlers can often reduce costs, save time, and maneuver more easily around congested job sites.
So when can a telehandler serve as an appropriate substitute for a crane?
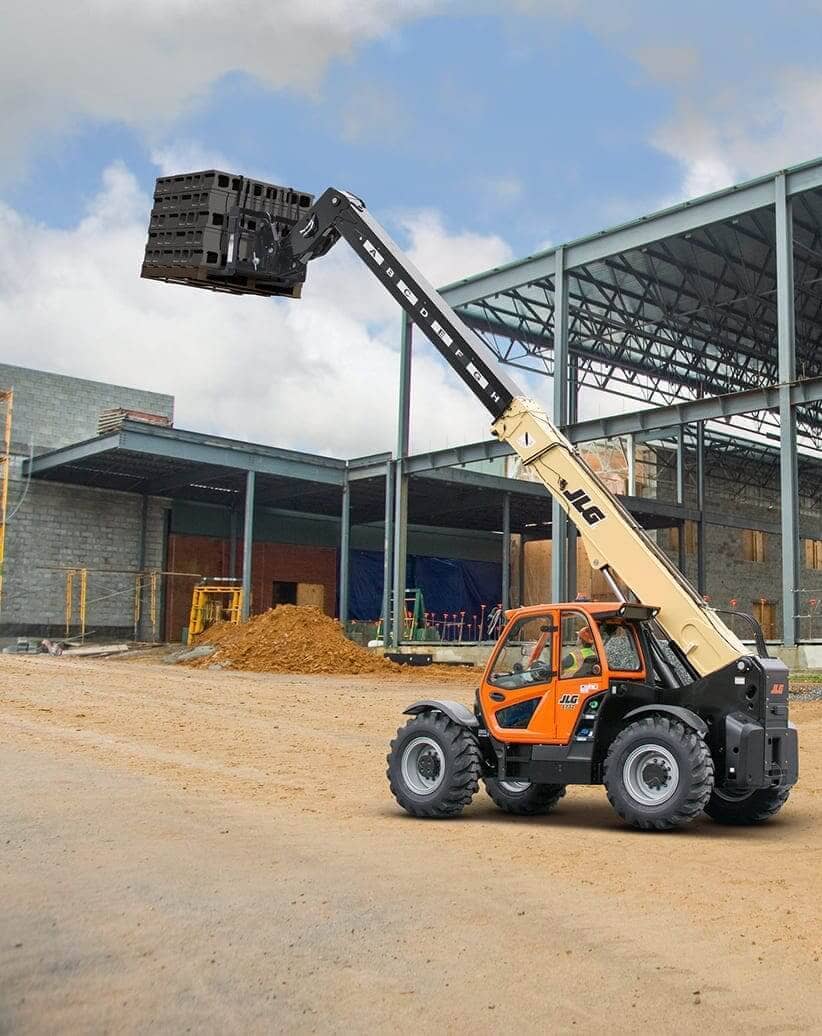
Mellott says there are five main factors to consider, which include:
- Weight of the load
- Distance to the target landing area
- Ground conditions
- Site access constraints
- Proximity to the public
There are several ways to determine if the telehandler is in fact capable of placing the load at the destination, Mellott says.
The first does not require the use of the machine at all. The telehandler’s load chart features an X and Y axis for distance from the front tires and height needed for placement. Using the load chart and a tape measure, a determination can be made to see if the machine can safely place the load.
The other way is through a dry run procedure. “The dry run procedure is a practice run of the lift or pick being performed but with no load on the forks” Using the indicators on the side of the boom, the operator completes a dry run placement and compares it to the load chart to determine if the machine can safely place the load, Mellott says.
Something else that contractors need to consider is that with the right attachments, some telehandlers can essentially turn into cranes. Though OSHA provided guidance on this in 2014, Mellott says questions about this issue come up in nearly every training class he teaches.
OSHA directive CPL 02-01-057 states, “Any forklift that lifts with a boom (including the boom of the forklift itself) and a hoist would be covered by the requirements of the cranes and derricks standard. For example, a variable reach forklift would also be covered by the cranes standard if it is configured with a hoist and used like a crane.”
This is important because that means the telehandler now requires a certified crane operator for its use, he says.
Selecting a Boom Lift vs. Telehandler with Work Platform
Not only is it possible for a telehandler to transform into a crane, it can also perform work like a boom lift when paired with a personnel platform.
When is this option a viable replacement?
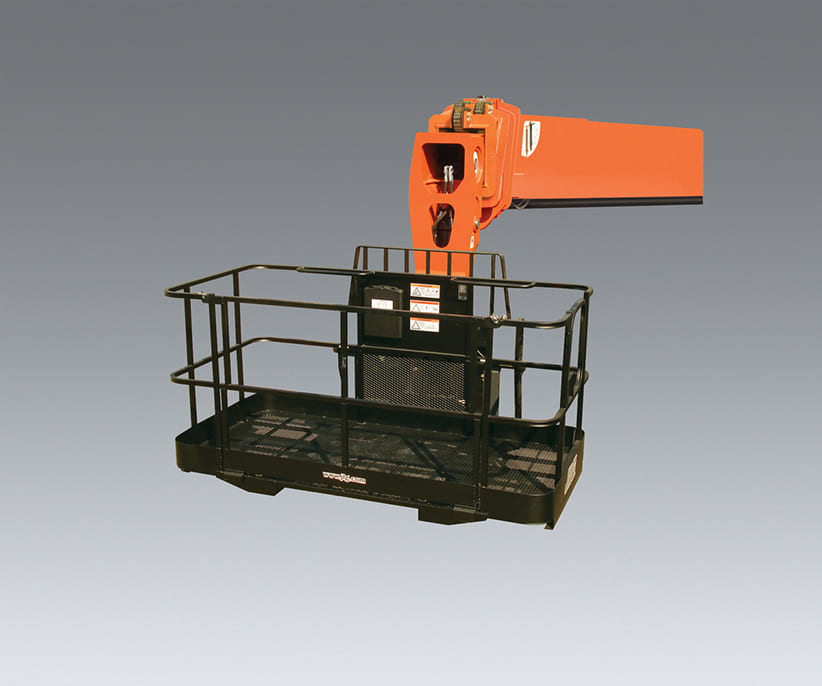
First, Mellott says contractors must ensure the work platform attachment is OEM-approved.
“All attachments, including the personnel work platform, must be an approved attachment,” he says. “They can't just stand on a pallet on the end of the forks.”
Contractors can check to see if an attachment is approved on the JLG website.
“On the JLG website, you can select a specific machine and locate the list of approved attachments for that machine,” Mellott says.
Second, the user must also take into account the distance to the work area, ground conditions, site constraints, and proximity to the public.
“Typically the reach on a telehandler is not nearly the reach that a boom lift can offer,” he says.
Telehandlers with personnel work platforms have the potential to pose additional safety concerns that contractors should be aware of, Mellott says. This is because the telehandler operator is located in the cab with personnel in the work platform, as opposed to a boom lift, where the operator is in the platform.
Telehandler operators need to maintain a clear line of communication and visibility with the personnel in the work platform, Mellott says.
MEWP Selection and Supervisor Training
On June 1, 2020, the new ANSI A92 suite of standards for mobile elevating work platforms, or MEWPs, went into effect. These brought sweeping changes to the design, safe use, and training requirements for MEWPs, which include boom, scissor, and vertical lifts.
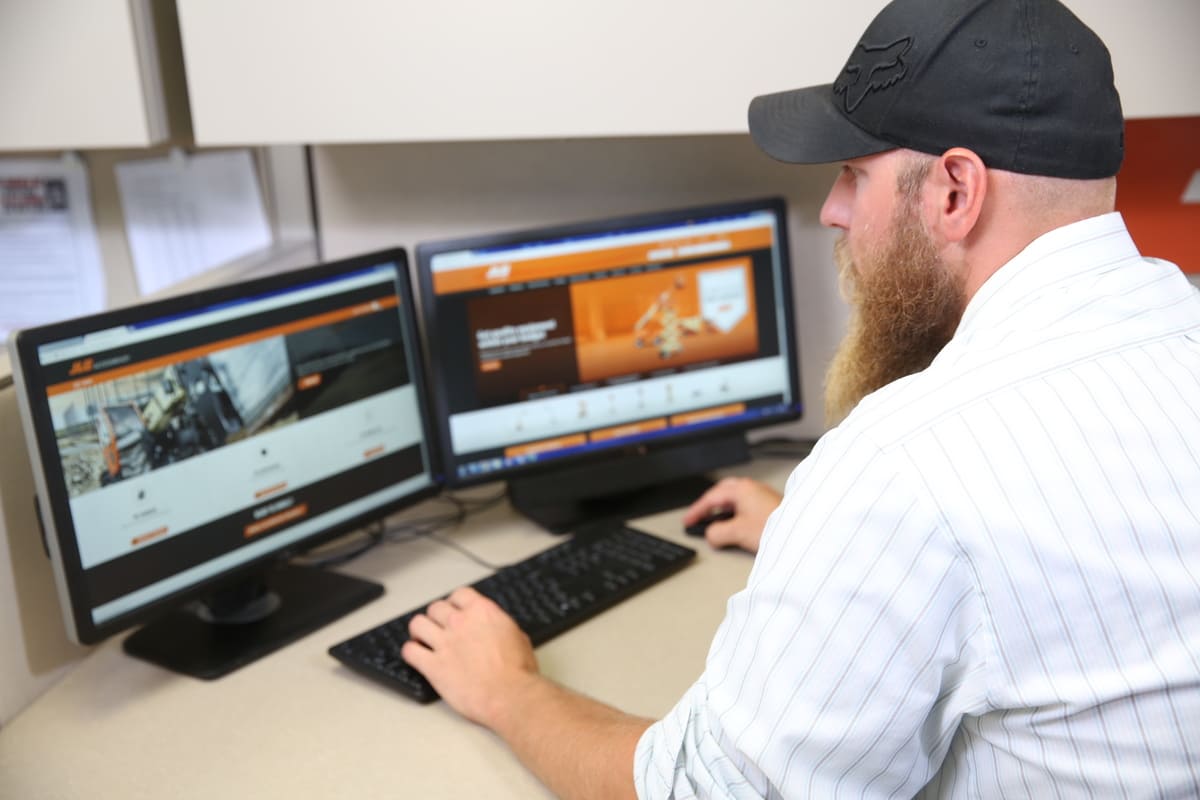
One new requirement in the standards is that supervisors, who are defined as an entity assigned by the user to monitor operator performance and supervise their work, must receive specific training. This training, available as an elearning course through JLG University, covers how to select the appropriate MEWP for the job, create a safe use program, and perform a site risk assessment.
Mellott says the Best Practices for Workplace Risk Assessment also includes some general guidelines on which type of MEWP to select, such as:
- Scissor or vertical lift: When the workers can be positioned directly beneath or beside the task to be performed
- Straight boom lift: When the workers need to reach a target that is in a straight line from the ground in order to perform their task (scissor lift with an extension deck may also be an option)
- Articulated boom lift: When the worker needs up-and-over reach, typically around an elevated obstacle, to access the task
Among the other factors that contractors should weigh are whether the machine has adequate height and reach for the scope of work and if it has the appropriate tires for the terrain, Mellott says.
Can Attachments Affect Access Equipment Selection?
If the work you need to perform requires specific attachments, it could impact the equipment you select for the job, Mellott says.
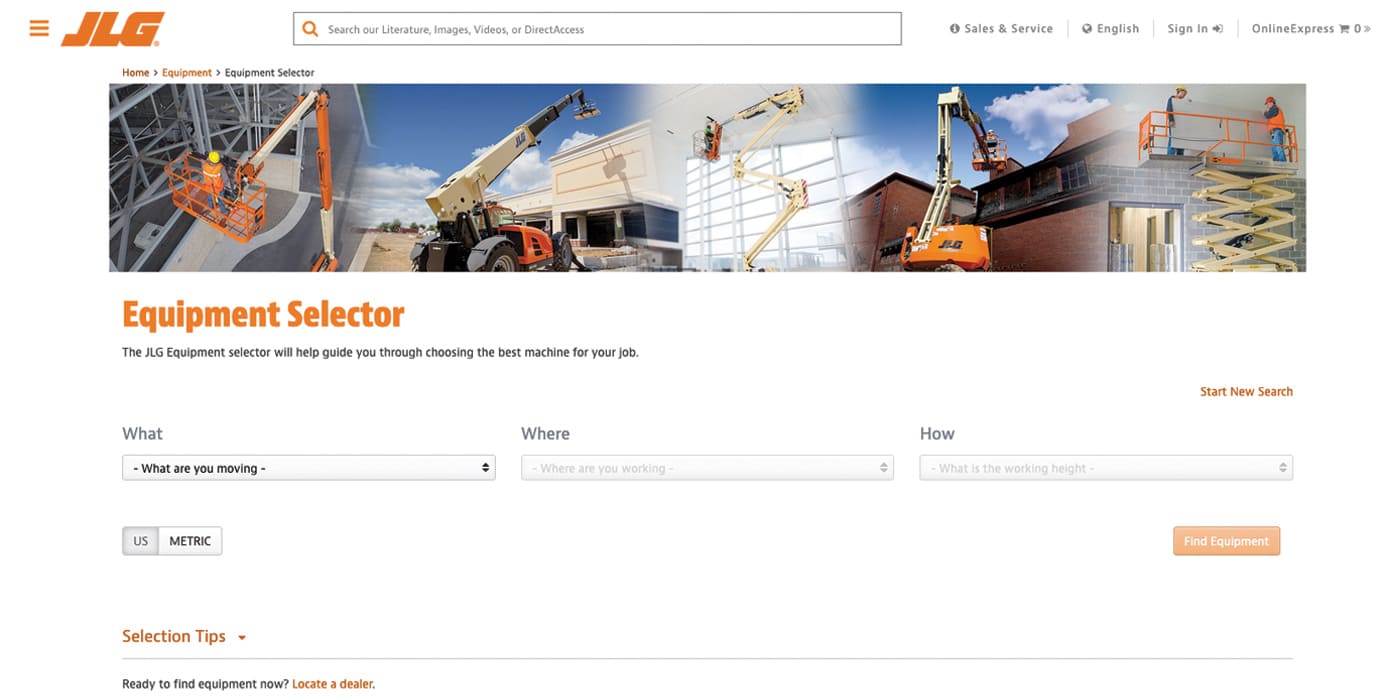
For example, an operator that needs to exit the basket to access work areas must choose equipment that pairs with a fall arrest platform. This is a special basket that has a cable on the exterior of the top rail, allowing a person to stay tied off while moving to a structure or another target, Mellott says.
“We also offer a bolt-on fall arrest option to upgrade certain boom lift platforms that were not equipped with it from the factory,” he says.
Ground-bearing pressure is another factor to ensure the surface can withstand the weight of the machine. Mellott says many users are not aware that there are decals near each of the wheels that detail the ground-bearing pressure of that machine.
“Every class I ask the students what it means and a lot of them think that it's what the machine weighs at that wheel,” he says. “It's actually the amount of pressure that wheel or that outrigger — whatever the point is that contacts the ground — could exert onto the ground.”
Attachments can also alter access equipment operation and functionality, Mellott says, with some requiring their own manuals that outline their safe use and other considerations.
For instance, a glazier kit for MEWPs will reduce the maximum allowable wind speed for machine operation, because glass panes can create a sail effect. Another example is that a welder kit for a MEWP could require recalibration of a boom lift’s load-sensing system.
Making the Right Choice
In addition to working with your rental company’s customer service representatives on your access equipment selection, digital tools can also assist in your decision-making.
Introduced at ConExpo-Con/Agg 2020, JLG’s Augmented Reality app allows users to view whether equipment can fit in an actual work area. Currently, boom lifts and scissor lifts are available on the app, with plans to add low-level access solutions and telehandlers by the end of summer 2021.
Project managers can also take advantage of the BIM library, which allows placement of 3D access equipment models in job site plans.
Finally, an equipment selector tool on the JLG website guides users to see what options pair with a particular task. To get started, users need to answer three questions:
- What are you moving?
- Where are you working?
- What is the working height?
“You drill down into each one of these areas, and it will show you what machines we offer that fall into those criteria,” Mellott says.
While many of these considerations may seem like common sense, Mellott says it’s important that access equipment users have a thorough understanding of what is unsafe and where to draw that line.
“We all have seen pictures online of people doing things that they're obviously not supposed to do with the machine that they had,” he says. “Many times these unsafe acts are a direct result of selecting the wrong piece of equipment for the job. Performing a proper analysis when selecting the appropriate machine is a great control measure to mitigate risks.”
Want to stay up to date with industry news and trends similar to this? Make sure you subscribe below to receive monthly updates from Direct Access with newly posted content so you never miss important information.